STRUCTURAL ENGINEERING
FINTON HOUSE SCHOOL
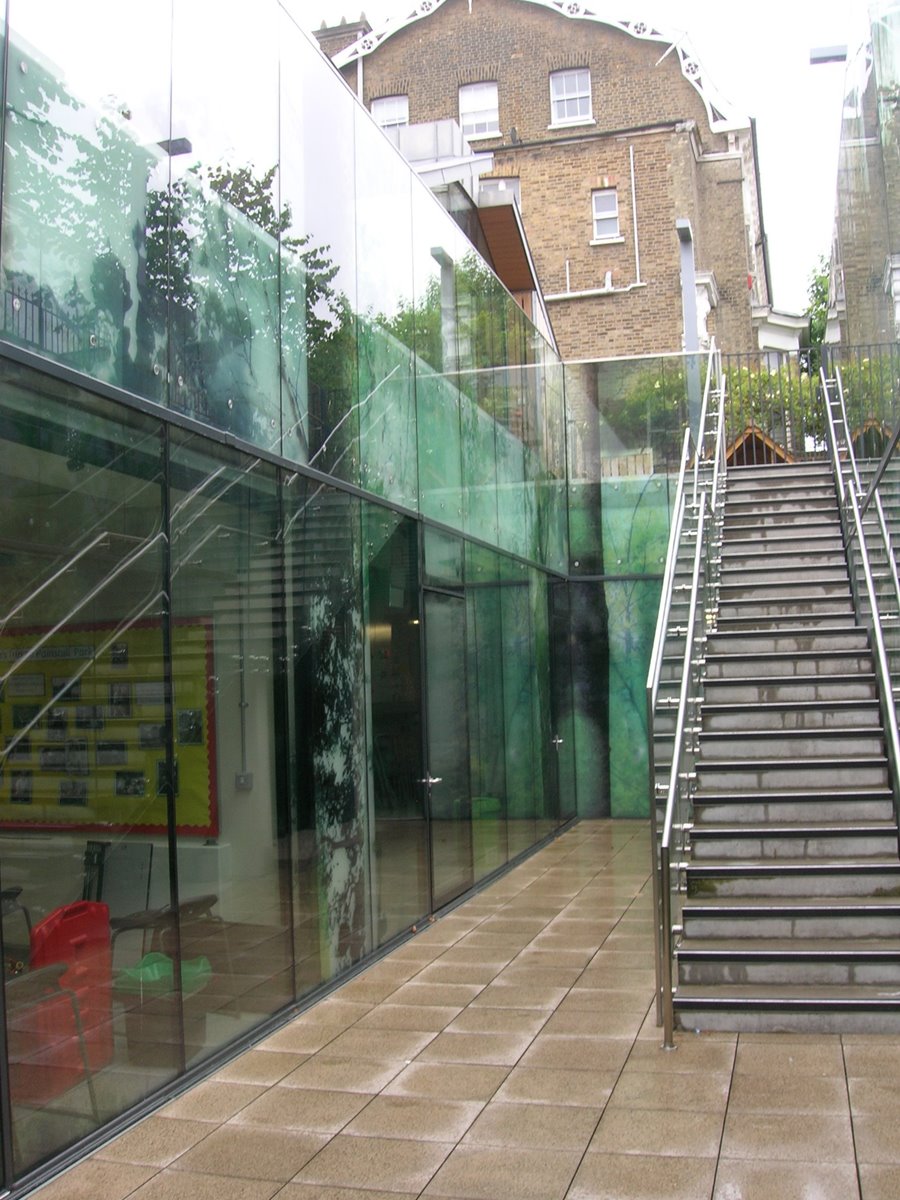
Finton House is a Preparatory School in south-west London, catering for around 300 pupils, including some with special needs, between the ages of 4 and 11. Housed in two large interlinked Victorian Buildings, which had already been extensively extended and added to, the school was running out of modern teaching space.
Located as it was on a constrained site in a residential area, Planning was sensitive. The project, therefore, was to go underground, under the playground to maximise the amount of space in terms of classroom size, but without taking away any playground space.
The design had to take into consideration careful investigation to ensure the water table would not be affected.
Disruption to local residents and the running of the school had to minimised and safety was of paramount importance.
The children now have a 400 sqm underground learning area featuring a glass-lined stairwell, decorated with trees, which directs natural sunlight into the classrooms, as well as their playground.
LOFTSPACE MEZZANINE – IMPERIAL HALL, CENTRAL LONDON
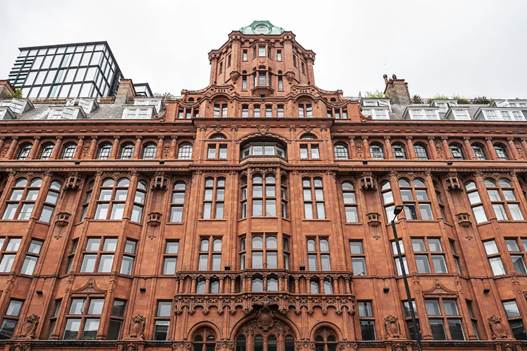
Our client’s apartment is located within the Grade 11 listed Imperial Hall in central London. Previously known as the Leysian Mission, it was built in 1903/1904, a landmark building in the area. It operated as a Methodist mission until 1983.
In 1998 the Leysian Mission building was converted into 30 apartments, 30 multi-level lofts and 9 retail units. The conversion and redesign had to respect the historic layout of the building and be in keeping with the Grade 11 listing. It was one of the first residential schemes in the area.
The apartment is one of the multi-level lofts dating from the 1998 conversion. Our client wanted to increase the floorspace of the apartment. To achieve this the existing mezzanine level would be extended and the staircase access to the mezzanine relocated. Before this could go ahead a reassessment of the loadbearing capacity of the existing supports for the original mezzanine and staircase access, needed to be carried out.
This showed they would not be adequate for the extended mezzanine floorspace and the relocated staircase, additional support was needed.
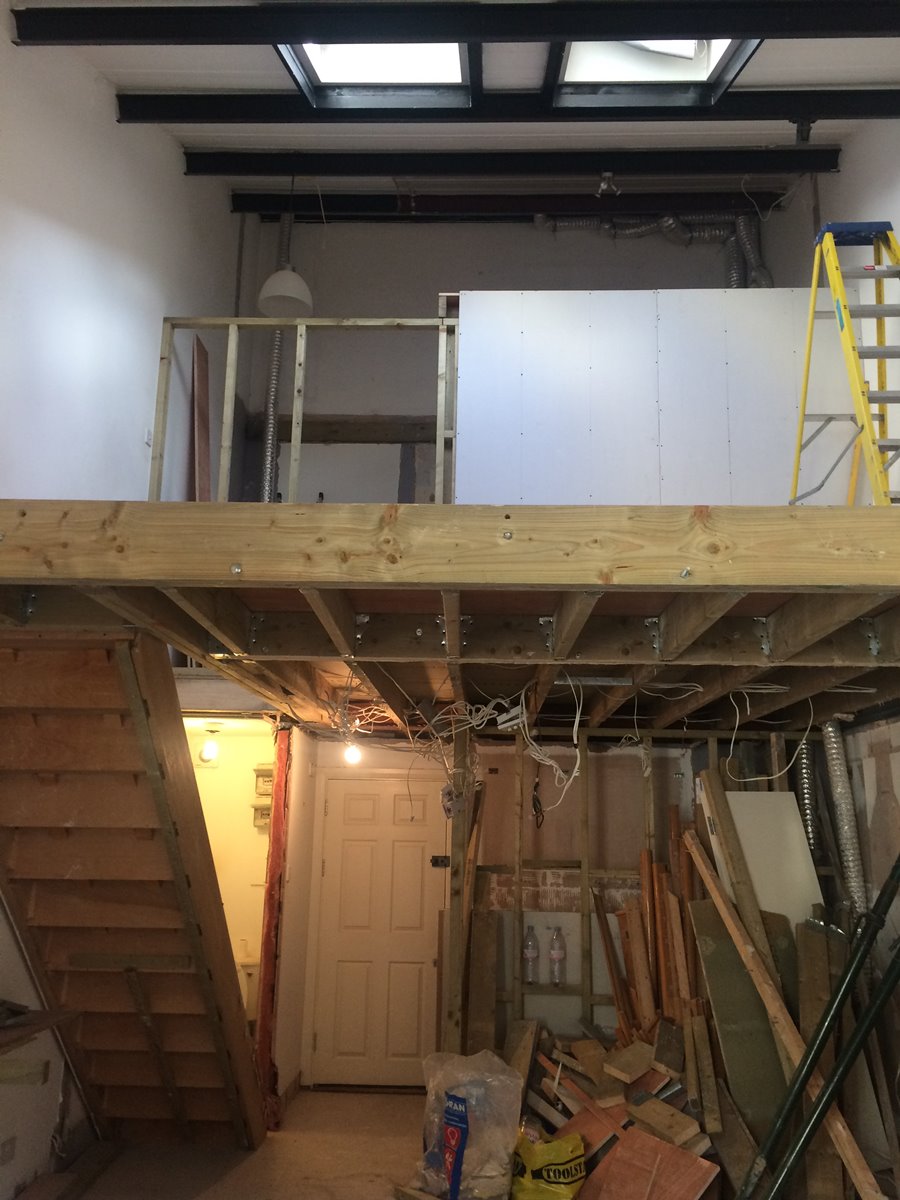
To provide additional support, we designed new floor timbers and a beam spanning the width of the apartment, for the extended mezzanine floorspace, as well as additional beams for the relocated staircase. The designs were incorporated in the building works, which were able to go ahead safely.
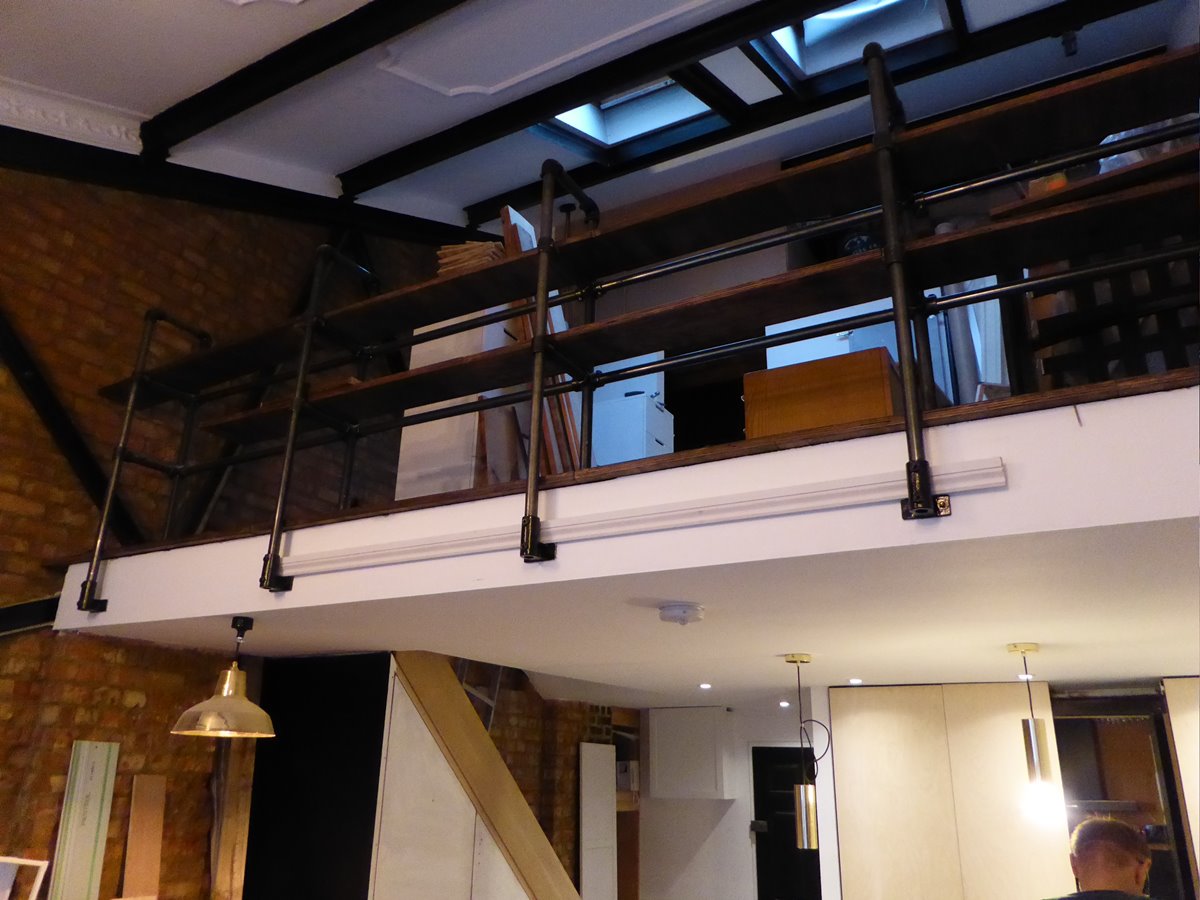
THE BELLEVILLE BREWERY
The Belleville Brewery is located in a small industrial park next to Wandsworth Common station. This microbrewery originated with a group of Dads raising funds for their children’s local school “Belleville”. As their children grew so did the brewery, it became very successful supplying beer to the local area. The company rented two units, one unit housed the brewing equipment and the other was used for storage. As part of their expansion plans they wanted to open a Tap Room where customers could drink the brewery’s beer. The storage unit had a mezzanine level which could be turned into a bar area. Before work could begin on installing the bar an assessment of the load bearing capacity of the mezzanine area had to be made. Having only been used previously for storage, the additional weight of the bar and its fixtures and fittings as well as customers, meant that the existing support for the mezzanine was not enough. We designed floor beams and columns to be constructed to bolster the support, so that the mezzanine would be safe for the customers to taste their beer.
The new tap room proved popular, so much so, the owners wanted to increase the public space. They focused on the ground floor area underneath the mezzanine bar area. To make the most of the space necessitated the removal of two walls. Before construction work could begin we had to assess whether the walls were load bearing or not and once removed whether the existing structural steelwork would be adequate to take the extra load. A thorough on- site-investigation concluded that the existing structural steelwork was enough, so building work could go ahead without a structural damage to the fabric of the industrial unit.